Hydrogen can be a clean fuel for heavy duty trucking. The target price for rapid adoption is $4-$5/kg, yet right now hydrogen costs $13-$16/kg at refuelling stations in California. Cutting the cost of making the hydrogen is proving slow. But Ted McKlveen and Bav Roy at Verne, writing for WEF, show that the production only accounts for 15% of the cost at the pump. Roughly 50% of the cost is from running the pump station (equipment like compressors and on-site storage) and 35% is from distribution (liquification and transport). To reach the $5/kg target, that’s where the focus should be. The authors describe how it can happen. They point at their new system that can densify hydrogen at 65% of the usual cost. Looking ahead, increasing the number hydrogen production locations and fuelling stations will decrease transportation distances. The amount of hydrogen that each refuelling truck carries can be increased. At the station itself, compressors and dispensers can reach lower cost simply from increased production volumes. New technologies can lower the required pressure for hydrogen fuelling. And innovation and standardisation in refuelling nozzles can drive cost reductions too. In other words, if 85% of the final cost of hydrogen is due to factors beyond production, that’s where the big cost reductions should be sought.
- Hydrogen is the most promising solution for tackling several hard-to-decarbonise sectors like steel production and heavy-duty transportation.
- But we must act to bring down costs across hydrogen’s value chain to ensure that it’s on a path to being cost-competitive.
- By targeting the 85% of ‘hidden’ and often-overlooked costs of hydrogen, we can enable it to achieve economic parity with diesel.
Hydrogen is the most promising solution to decarbonise several difficult-to-decarbonise sectors, including steel production (8% of global carbon dioxide, or CO2, emissions) and heavy-duty transportation (12% of global CO2 emissions).
Indeed, the US Department of Energy believes hydrogen can play a role in decarbonising 25% of global energy-related CO2 emissions. But more work needs to be done to reduce its costs.
Here’s what needs to be considered in order to ensure we develop hydrogen’s full value chain to ensure that it is on a path to being cost-competitive with diesel.
Efforts to make hydrogen production cheaper
There has been sustained focus on driving down the cost of hydrogen production to make such hydrogen applications economically viable.
In the United States, the Inflation Reduction Act introduced a lucrative tax credit – worth $3 per kilogram of zero-emission hydrogen – to encourage construction of new hydrogen production facilities.
Globally, investors have poured more than a billion dollars into electrolyser startups like Electric Hydrogen, Ohmium, Verdagy and EvolOH that promise to bring down the cost of green hydrogen production through innovation and scientific breakthroughs.
And more recently, naturally occurring “geologic hydrogen” has seen significant investment, as it promises another route to lower the cost of hydrogen production.
Investments in hydrogen production are important: current clean hydrogen prices are too high and too variable for adoption by end-users.
However, solely investing in hydrogen production is not sufficient to make hydrogen a viable option in sectors like heavy-duty transportation. The entire supply chain – from production to end-use – must be addressed to minimise the cost of hydrogen.
Where the hidden 85% of hydrogen costs lie
Researchers at the Argonne National Laboratory in 2019 determined that hydrogen production costs account for just 15% of the final cost “at the dispenser” for hydrogen used in transportation.
The remaining – or “hidden” – 85% of hydrogen costs often get overlooked, but these costs must also be reduced for hydrogen-powered heavy-duty transportation to achieve economic parity with diesel.
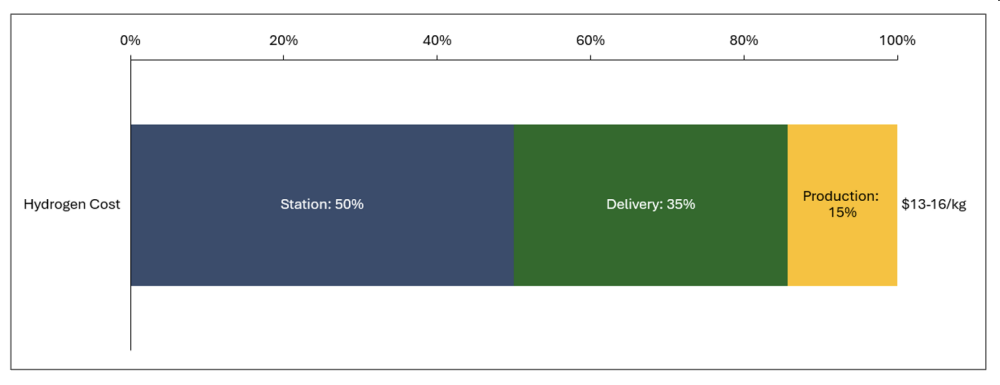
Production accounts for just 15% of hydrogen costs / IMAGE: Data from the Argonne National Laboratory, chart from Verne
At the time of the Argonne National Laboratory study, hydrogen cost $13-$16 per kilogram at refuelling stations in California.
On a cost per kilogram basis, just 15% of this cost is due to production (~$2/kg). Roughly 50% of the hydrogen cost is from the station (equipment like compressors and on-site storage) and 35% is from distribution. This means a staggering 85% of the final cost of hydrogen is due to factors beyond production.
Heavy-duty trucking stakeholders, from fleet owners to original equipment manufacturers (OEMs), often cite $4-5/kg as the required price of hydrogen for hydrogen trucking to reach cost-parity with diesel. So clearly driving down the cost of production is insufficient to reach the cost target needed to spark hydrogen uptake.
Invest to bring down hydrogen costs
While the cost of hydrogen production can – and will – vary depending on a host of factors, the takeaway is clear: we need to invest in bringing down the costs of hydrogen delivery and refuelling.
Thankfully, there are clear pathways to reduce hydrogen delivery and station costs.
1. Hydrogen delivery costs (35%)
Delivery cost is driven by two factors: densification of hydrogen at central production facilities (e.g., hydrogen liquefaction), and delivery of hydrogen to fuel stations via trucks.
Centralised hydrogen liquefaction can add $2.75/kg to the cost of hydrogen: a meaningful number within the context of the $4-5/kg total cost target.
Our company, Verne, identified this cost driver and built a system that can reach comparable hydrogen densities at 65% lower cost, unlocking the high densities needed for distribution with much lower energy costs.
The truck transport costs for hydrogen will also come down over time: as more hydrogen production plants are built, the average distance between production locations and fuel stations will decrease, bringing down delivery distances and costs.
There is also innovation occurring to increase the amount of hydrogen that each truck can carry, maximising the efficiency of each trip and decreasing the number of delivery trips required.
2. Hydrogen station costs (50%)
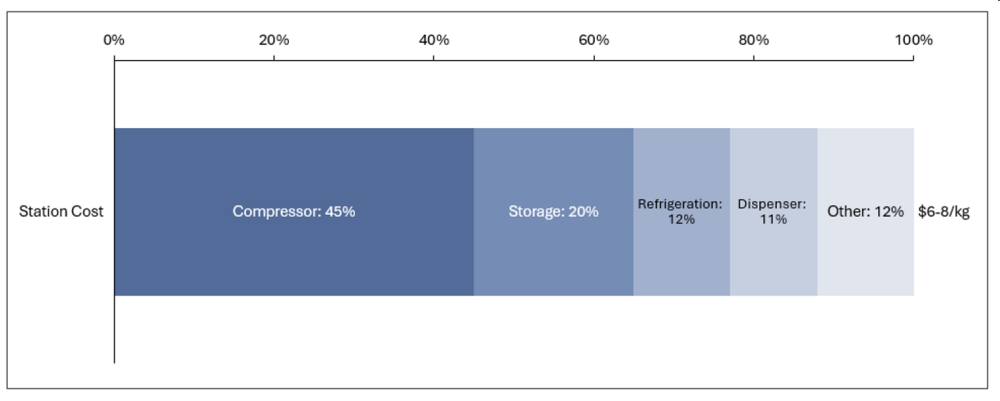
Breakdown of hydrogen station costs, including compressor, storage, refrigeration and dispenser / IMAGE: Data from the Argonne National Laboratory, chart from Verne
Hydrogen station technology likewise has clear pathways for cost reduction. Several components, such as compressors and dispensers, can reach lower cost simply from increased production volume. Innovation in compressors can further reduce costs and increase reliability.
Verne is also addressing station costs, with new technology that lowers the required pressure for hydrogen fuelling, reducing the cost of high-pressure compressors. Utilising lower pressure also increases compressor reliability and up-time, a major source of frustration for hydrogen users today.
In addition to the compressor, it is also critical to drive down the cost of refuelling dispensers (>10% of station costs). Innovation and standardisation in refuelling nozzles can drive cost reductions and maximise ease-of-use for fleets and truck drivers.
Driving down the cost of hydrogen
For hydrogen to reach its promised potential in difficult-to-decarbonise sectors like heavy-duty transportation, the all-in cost of hydrogen must decrease.
This cost reduction will be enabled by increased investment: just as in hydrogen production, new approaches and technologies are required to optimise refuelling and distribution.
Coordination between infrastructure developers, OEMs, governments, research laboratories and startups will also be important to ensure that the most innovative, cost-effective equipment and methods are standardised and commercialised.
Investing in cost reductions across the entire hydrogen value chain, and not just in hydrogen production, will enable hydrogen to displace diesel fuel and usher in a new era of heavy-duty transportation.
***
Ted McKlveen is Co-founder & Chief Executive Officer at Verne
Bav Roy is Co-founder & Chief Operating Officer at Verne
This article is republished in accordance with the Creative Commons Attribution-Non Commercial-No Derivatives 4.0 International Public License
- SEO Powered Content & PR Distribution. Get Amplified Today.
- PlatoData.Network Vertical Generative Ai. Empower Yourself. Access Here.
- PlatoAiStream. Web3 Intelligence. Knowledge Amplified. Access Here.
- PlatoESG. Carbon, CleanTech, Energy, Environment, Solar, Waste Management. Access Here.
- PlatoHealth. Biotech and Clinical Trials Intelligence. Access Here.
- Source: https://energypost.eu/hydrogen-too-expensive-for-trucking-85-of-the-cost-is-getting-it-to-the-pump/