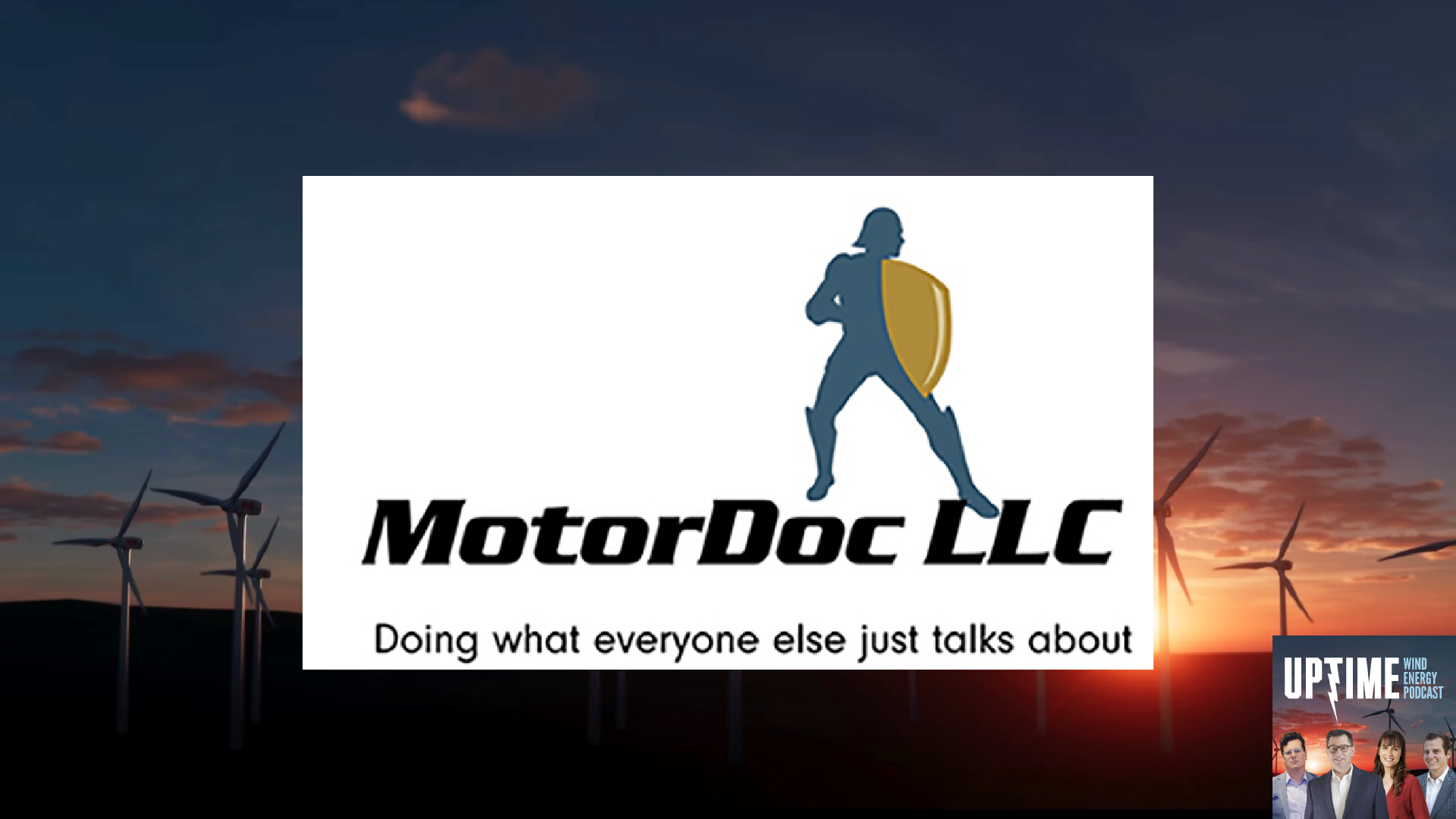
Podcast: Play in new window | Download
Allen Hall interviews Dr. Howard Penrose, president and founder of MotorDoc LLC, about the groundbreaking EmpathCMS electrical signature analysis system. Dr. Penrose explains how the technology can quickly and non-invasively detect developing faults in wind turbine components like generators, gearboxes, and bearings, helping to optimize maintenance and prevent unplanned downtime.
Sign up now for Uptime Tech News, our weekly email update on all things wind technology. This episode is sponsored by Weather Guard Lightning Tech. Learn more about Weather Guard’s StrikeTape Wind Turbine LPS retrofit. Follow the show on Facebook, YouTube, Twitter, Linkedin and visit Weather Guard on the web. And subscribe to Rosemary Barnes’ YouTube channel here. Have a question we can answer on the show? Email us!
Pardalote Consulting – https://www.pardaloteconsulting.com
Weather Guard Lightning Tech – www.weatherguardwind.com
Intelstor – https://www.intelstor.com
Allen Hall: Welcome to the Uptime Wind Energy Podcast. I’m your host, Allen Hall. Our guest today is Dr. Howard Penrose, the president and founder of MotorDoc LLC, and the creator of the groundbreaking EnPath electrical signature analysis system. Dr. Penrose has over 30 years of experience in the field, authoring books, presenting at conferences worldwide, and providing training and consulting services to numerous industries, including wind energy.
The Empath system Dr. Penrose developed is a cutting edge tool for condition monitoring and predictive maintenance of electrical assets like motors, generators, and transformers. By analyzing the unique electrical signatures of equipment, Empath can detect developing faults early, preventing unplanned downtime, optimizing maintenance, and extending equipment life.
Howard, welcome to the program.
Howard Penrose: Thank you very much. And I just have to correct you on one thing. And that’s the Empath system was actually originally developed at Oak Ridge National Labs and is is, construct, is basically built and maintained by Framatome ANP, which is International Nuclear Power Company.
We are their non nuclear distributor and researcher. Large portion of what we do at MotorDoc is research the applications for electrical signature analysis and develop the algorithms.
Allen Hall: So this is, we have a magician here today, so to speak, because the whole thing about wind energy and when you talk to the engineers is the vast majority of them are mechanical engineers.
Drivetrain, blades, right? They know a lot about how the turbine works mechanically. But it is an electrical machine. It’s there to produce electricity. And that means there’s a lot of electric motors and obviously one big generator on the turbine. And that’s the heart of the system. And that’s the part that we really need to work.
What? I think you guys have done is interesting because you’re using the generator to diagnose things that are happening onside the turbine that are not only electrical, but mechanical. You want to explain how that works a little bit?
Howard Penrose: Okay. Well, with vibration analysis, for instance, I will use an accelerometer with a piezoelectric cell or some of the newer technologies that involve etching and certain other things of materials. And you put that on the casing of a machine, and you generate an electrical signal signal in that component, that accelerometer, for instance, or whatever other type of device it is for vibration. So you have to read all the movement of all the components inside the machine through the material.
through that transducer into something else that then translates that data in, either as a rules based system using squiggly lines or a machine learning based system, that kind of thing. Electrical signature analysis is exactly the same thing, except we use the air gap of the machine, whether it’s a generator or a motor or a transformer, as our transducers, the little magnetic field.
In between the components, not the rotor, not the stator. And we gather that information through just straight voltage and current. So the voltage and current comes out we use that and translate it in exactly the same manner we do with vibration. Matter of fact, most vibration analysts will recognize most of the signatures we look at when we’re looking at squiggly lines.
The difference is you have to cross your eyes and stand on your head, but that’s about it.
Allen Hall: So the Empath system, from what I’ve seen online, it measures a couple of voltages and some currents on some wires, which maybe you can describe what you’re actually measuring there.
Howard Penrose: If we’re doing the generator in a wind turbine we’re measuring the voltage and current directly off the stator.
If we’re doing the generator in a wind turbine we’re measuring the voltage and current directly off the stator. So if my transformer is uptower, that data has to come from uptower. If the data, if the transformer is downtower, say in a GE or some of the other machines, I can take that data downtower, which I prefer, to be perfectly honest.
But the idea is you go in you clamp on to three phases of current and three phases of voltage for optimal voltage. analysis. Really, if I’m just analyzing the components, I just need one good phase, right? One, one sinusoidal phase. There’s a lot of things that happen electrically in a machine, in a wind turbine, that are odd as compared to other types of generators.
So we have to work with that. And of course, whether I’m looking at a DFIG I like to call certain designs S FIG. Where I don’t have a feed to the rotor, I just have a switching system, such as in the old Suzlons. Or whether it’s an induction machine or a permanent magnet machine, each one is handled just a little differently, although the signatures are the same.
Allen Hall: So you’re measuring three voltages, three currents. On those signals is the power that’s coming from the generator, basically. But there’s other things on top of that. What electrical signals are on top of that, those power signals?
Howard Penrose: Every movement, every torsional issue, every component from the transformer to the blades.
In a defig even in some of the newer ones and one or two older designs that have the dual planetary gear set. We just added this as a matter of fact, in American clean power, we just add the, into the gearbox playbook, electrical signature analysis is one of the prognostics for the gearbox.
Through the air gap, we get to see. The transformer, we get to see all of the components in the generator that includes the bearings the Y rings and the rotor, which that’s, I think that’s one of the most popular reasons that were used is to define fracturing Y rings, and we’ll see those 14 months out.
And then even wedge issues of either vibrating or missing wedges in certain stator designs. Then we’ll see coupling issues. We’ll see all of the bearings in the gearbox, including the planetary bearings. We will see all the gears in the gearbox. I can’t tell you if it’s broken, cracked, or whatever, but I can tell you that there’s something wrong.
And not only that, I can tell you how much energy is being lost across that defect. And then the main bearings, we’ll even see when we have lubrication issues. One of the most common is when the lubrication is not changed out properly and you get dried grease at the bottom. We’ll read that as an outer race signature.
And then finally, if the blades aren’t aligned right, they don’t, they’re not turned correctly within a couple of degrees. We will see that as a blade pass as the impulse as it, as each blade passes the tower. You’ll see that variation, which can get tricky because certain designs now start to turn the blade a little bit based upon wind gusts and what LIDAR picks up coming at the wind tower.
Just by the way, what we didn’t include is the fact that I’m the chair of standards for ACP for wind. In the United States. So yeah, I have a little idea of what’s going on with the turbines.
Allen Hall: Just a tiny bit. Now, let me give a little, just talk about your background just for a second here, because I think it’s important.
You’re you started in the Navy. You’re from, originally from Canada, right? You came to the States and then you enlisted in the Navy.
Howard Penrose: I’m dual. So I was born in Michigan while my dad was finishing his doctorate at University of Michigan. Then he headed up the fisheries department in St.
John’s, Newfoundland, which makes me an official Newfie. So I joined the Navy. My worst class in A school was electric motors and generators. So I decided it was going to be my best subject. As I was one of the first hundred on board the Theodore Roosevelt, an aircraft carrier, and they said, what do you want to do?
And I said, I want motors. And generators. I was a a conventional electrician, not a nuclear power electrician. So they put me down there and, um, basically being one of the first hundred, I knew everybody. As a matter of fact, the nickname MotorDoc came from the captain of the ship back when I was 19 years old.
He authorized me to become the youngest electric motor repair journeyman in the Navy ever. I think to this day, so you have to sign up for six more years to get it. I didn’t have to I went to motor rewind school. I went to all the theoretical schools. I was enlisted. I got meritoriously advanced through E5 by the time I was 20.
So I spent two years in a chief’s position running a motor repair shop as a journeyman on an aircraft carrier.
Allen Hall: It takes a person like you that has the hand on hands on experience. Plus, a little bit of book knowledge, plus some education, and then have that kind of percolate for several years to go, okay, there is something to electrical signature analysis, and it’s real and to decode it.
I think that’s the hardest part, is decoding what’s there.
Howard Penrose: That, that is exactly the most challenging part, and the part, and the reason why most companies that have attempted to do it have failed is two parts. One is they’re trying to do it with current signature. I’m sorry, but a generator does not produce current.
It produces voltage. Wind is definitely different in that it’s both. There’s times when it acts because of the rotor, it’ll act as a load, times when it’ll act as a generator. And then with all of the controls for VAR correction, voltage correction, things like that. It will do different.
Wild things. The good news is I don’t care. What I do care about is that is that, for those who attempted the technology, not understanding that the technology measures the speed of the magnetic field, not the physical speed of the rotor. I don’t care. So if I’m a vibration analyst, I need feedback as to how fast the rotor is turning.
If I’m doing electrical signature, I need to know how fast the field is turning. Because in order to, in a defig, to get 60 hertz out, my field, if it’s a six pole machine, which a majority are six pole, others are four pole, that’ll be 1200 or 1800 rpm. If it’s a, if it’s a 1200 rpm, it’s going to be running slightly over 1200 rpm, which is why you don’t get exactly 60 hertz, right?
Because if you ran it exactly, then it becomes unstable, so you have to have it, yeah, you have to have it over speed just a little bit. That 1200 RPM motor, I’m just, I’m actually working on 320 turbines before we got on the call. The actual physical speed might hit as high as 1500 RPM, right? But if it did, and I didn’t compensate for that speed, I would have something like 80 Hertz.
Okay. Yeah, coming off, and it would fly all over the place. Then I would have to control it. But one of the, one of the, magical bits about D Fig is the VFD that runs in parallel and feeds the rotor changes either if it falls under that 1, 200 RPM, speeds it up, and if it’s over, slows it down.
One of the things we had discovered because of industrial work in active front end drives, which don’t have a DC bus, we can read through it. A motor that’s running at 35 hertz, on the incoming side, we discovered that all the signatures would be as if it were running at 60 hertz. If it was running as if it was on just a regular power source.
So I applied that to electrical signature. I applied that with electrical signature analysis to wind turbines. And suddenly we were seeing everything.
Allen Hall: So with that, you can see a lot of. noise or frequencies inside of that. You sampled it high enough now that you can start investigating, look inside of that data and you don’t need a lot of data.
You don’t need a lot of time. You don’t have to sit there and analyze data for hours. One set of data. Exactly. And that’s part of the key.
Howard Penrose: Now, this is a rules based system, right? Now we will, if we’re doing continuous monitoring, because we have that capability and we’re working on a capability with some of the OEMs to be able to just take data right from their towers, so we don’t have to have hardware.
to do the analysis. But we need a sample rate of a minimum of 10 kilohertz in order to be able to separate things out. And when we fall below that, the load has to be way up on the machine. The prognostic machines that are at that take data at 7, 500 hertz or less, they have to have wind speeds of at least 10 meters per second to be able to see anything.
We’re seeing it right at cut it. Which is bad. really interesting.
Allen Hall: A lot of machines take data faster than that. 15 kilohertz is what I’m here. Some of them are doing at the minute. So there’s enough data there.
Howard Penrose: But when they do 1500 kilohertz, they had, they only have very small data sets. So they switched that frequency so that we can get a longer data set.
The length of time combined with that that sampling rate is what gives us the resolution. And then because we’re doing 12 kHz, that also gives us a 6 kHz FMAX. That means we can see out to 360, 000 CPM. And most everything on a wind turbine happens under 3, 000 Hz.
Allen Hall: Oh, easy. Yeah. So that’s, and there’s your magic, right?
Now you’ve sampled the data fast enough and long enough to analyze essentially anything that’s happening on the wind turbine. What you’re measuring voltage wise and current wise all that data comes in. You then, I’m going to use some fancy terminology and I promised myself I wasn’t going to do this, but here we go.
They basically take a Fourier transform, right? So you’re looking at it in the frequency spectrum versus the time spectrum. And what that does, you start looking at rotating machines. They’ll start having peaks at certain frequencies based upon the mechanical principles in which they were designed. And then Howard, you come in and go.
That is a bearing, or a gearbox, right?
Howard Penrose: Yeah, and the nice thing is, the formulas are exactly the same. The multipliers for a bearing are the same as what I’d use in vibration. For instance, our technology we have a library of bearings in there with everything preset, so I don’t have to sit there and calculate out all the angles and number of balls and what the cage looks like and all that other crazy stuff that we learned in, in vibration school I just pull it out of a, out of a thing and the same thing that you do for, the multiplier time one RPM is the same multiplier times one Hertz.
Yeah, so we, you get the one time multiplier and you plug it in and you can identify inner race, outer race, ball, or cage. The nice thing about ESA is I don’t get harmonics. I just look at the one time. For that value, just like if I have a rotor related issue, like for instance, somebody asked me, could I detect a failing Y ring with vibration?
I said, absolutely. But you don’t have the bandwidth to do it. It would take too much memory because you would have to look out at four times the four times the. Slot frequency for the rotor, for certain aspects of the failure. Yeah, you’d have to in vibration. You might get lucky and see some pole pass frequency sidebands, which are twice the slip frequency.
But that would be mechanically related versus electrically related. So that’s going to constantly vary.
Allen Hall: So let’s talk about the wiring for a moment. So a wiring is, from simplistic terms, is how a connection internal to a motor that makes the thing spin.
Howard Penrose: Wound rotor generator.
Most wound rotor motors just have a connection made. they don’t have a ring. So in, in defigs, they normally have an actual ring like a hoop, and that goes around, and then they’ll have tabs that connect into it. Some will have direct connections. We’re working on some of those now. But what we discovered first off, we were asked by Chris Petrola from Axiona, and he did a whole presentation on this.
So I dare throw him into the weeds. He’s now with the now and he’ll appreciate it. But he had us go up to Calgary. He called me one day and I happened to be when he called on an overhead crane and a steel bell testing a wound rotor motor for failing slip rims. So we were testing, while everything’s moving, we’re over the pit of steel, a hundred feet up, staring down into molten, whatever, and he calls.
Of course, he called, so I had to answer. And he goes Hey, have you ever detected failing connections in the rotor of a defig generator? And I go, No, but I have a theory . So we go, we went up to Calgary to an to an Axion site, tested 40 turbines. He produced this at awe at the time, now a CP in 2018.
Because we did it in 2016, and then the repair shop out of Quebec went there Dallon, went there and and replaced the Y rings and took pictures of all of them. Now, of the 40 turbines, we detected 20 of them with fractured Y rings, and one, I said, I had a questionable reading. And that turned out to be a partial fracture.
They detected this, and then one year later, after we had detected them, Wind through the machines and pulled out the Y rings and replaced them up tower.
Allen Hall: Okay, so this is the key here. So not only are you able to detect problems in mechanical equipment and electrical equipment, for that matter, early, and diagnose, like, where it is health wise, it can be done so quickly, you can do most of a farm in a day.
Howard Penrose: So from 2017 to present, and wind is only about 20 percent of our work. I personally have been on over 4, 000 turbines collecting data, mostly in the US, some Canada. However, the technology is being used right now heavily in Brazil, Mexico, Canada, US. Asia and just a little bit right now in Europe, definitely in the Middle East too.
Allen Hall: Sure. Anywhere there’s a motor or a generator, you’re there.
Howard Penrose: I’m just talking about wind turbines. As far as the technology goes, it’s being used globally. The Empath system is one of the best kept secrets out there. We’re replacing vibration equipment in the industrial side, all over the place.
Monday, I’m dropping off. enough to for Reynolds aluminum to finish replacing all their vibration equipment with over 400 of our systems.
Allen Hall: Okay. See, this is where I first ran across you. I was on a wind site talking to a site manager. And I was saying, Hey, what’s cool. What’s the cool thing you’ve seen?
And the response back was, have you seen MotorDoc? Those, that equipment came in and they diagnosed every motor generator problem, gearbox problem, bearing problem. We had on each of the turbines and a couple of minutes, literally a couple of minutes, and we started to dig. We thought okay. Maybe? So we dug into them and they were 100 percent right.
Howard Penrose: I like hearing 100%. I usually tell people 85 to 90%. Even though the EPRI study that was done, looking at the technology and Empath was top. We were seen as well over 90. Closer to 95%.
Allen Hall: I think if you guys is one of the, I don’t know, one of the best kept secret, cause you’re not a secret. You’re out there doing tremendous work and OEMs know of you, operators, some operators know you very well.
Howard Penrose: OEMs, Almost all of the OEMs use us, meaning have, they have our equipment but we don’t put the names of our customers on our website to brag. We’ve actually been word of mouth for, 10 years. Really? I’ve been using the technology on wind. For over 20, since I think 2003 was my first set of towers in the Mojave desert
Allen Hall: But that’s that’s an amazing piece to this I think your story Is that you’ve done your homework and you’ve been in industry a long time you understand The physics i’ll call it associated with wind turbines motors generators that electrical machines that then You can then used to happen 40, 50 years ago, when I was a kid that those people were around all the time.
You could walk into a motor or a winding shop and people knew how these things worked and we’ve lost some of that. So you’re the part of that architecture of your, that kind of carryover into, hey we already know this stuff. Now we just need to apply some common sense to it and use it to our advantage, which is what you’ve done.
Howard Penrose: Yeah and we continue to do it. People go why aren’t you worrying about how many you sell? It’s I have no overheads. I don’t have a hundred people that I have to pay. I just, there’s only a handful of us. And with all the systems we have in the field what we do is we work ourselves out of work by building all the rules into the software.
We know that intrusive maintenance introduces faults. So everything we do, we try to do as non intrusively as possible.
Allen Hall: This is why you’re on the podcast, because I want to make sure that the select portion of the world that doesn’t know you exist then finds you. Because it’s a quick diagnostic tool, and that’s, and that was the input I got from the O& M people.
People operation maintenance people is that it’s a huge help. It’s such a simple device. They plug in you get the data it analyzes it doesn’t take a lot of Hand holding there Usually as soon as the data pops up it tells you exactly what it sees Right and you always have Howard to call if you get confused, but basically that thing tells you what’s wrong Quickly, and then you can go debug your turbine, or at least have a health status on your turbine, a real health status on your turbine without a lot of work.
That’s genius.
Howard Penrose: It reduces the wear and tear on the technician, right? They’re not climbing to to do other things. One of my good friends now from, the engineer from from H& N, Hank he got up and he explained how boroscope testing for the detection of the wiring issue is only about 50 to 60 percent accurate because you’re looking to see if something’s broken, like the insulation is broken, plus you can’t see the tabs and everything else.
We’re seeing partial fractures long before that occurs. And like I said, Up to 12 to 14 months out. So I’ll usually give it an A through F. Nobody gets an A, but a B through F I’m a horrible professor, but no, no waiting. Those grades. No, B just means continue monitoring. I don’t want people to not check because we have seen like Brazil they’re now just so you’re aware of the wiring issue and everything else.
We were the ones who discovered that was, along with Shermco and H& N, it was a joint project that it was actually fatigue, it’s not a problem with the design of the wiring. It has to do with a a subsynchronous resonance that exists on the grid. So the windings are constantly moving. They’re constantly flexing ring.
Shermco had taken sections of a ring and had a metallurgist look at it. And we could see all of the fatigue points.
Allen Hall: People don’t think of electric machines having fatigue, right? They just think them as just a bunch of coppers spinning around.
Howard Penrose: Everybody since the dawn of time thought that all of these mechanical issues were strictly mechanical.
And we’re finding that there’s electrical reasons for a lot of the mechanical conditions and there’s possible solutions to them. In fact, some of those solutions have already been worked on. But not for this reason.
Allen Hall: And that’s what I think that’s the point, right? Is that we’re in some measure, we have old technology, proven technology, but we’re changing it drastically in the way that we feed it.
Howard Penrose: From both directions, it’s not just the power generation, but we spend a lot of time on in the industrial side is what the heck they’re putting back in the system and utilities, we’ll go in, we’ll see these horrible harmonic conditions in power. ground and neutral. And we’re trying to correct it and the utilities are all going we don’t care about that.
It means nothing. We don’t bill on that. No joke. It’s wait a minute, this is actually consuming a ton of energy. Plus it’s really dumping a lot of garbage back into the system that works its way all the way back because While the transformers and certain filters take some of it out, I can go onto the bulk grid and see some of those oscillations.
Allen Hall: And that’s if you’re a wind turbine operator and you’re living with these conditions, you wouldn’t, your first thought is there’s something wrong with the OEM equipment that I purchased. I need to go debug this thing. But the mere fact that it’s connected to the grid may be driving the problem on the turbine.
And we don’t think about it that way. We think about turbine out, not grid in.
Howard Penrose: Yeah. And then a combination of, Some of the sites will do VAR correction or voltage correction and they’ll be correcting for their site next door. You know what I mean? So one site won’t be doing it, the other site will depending on the controls.
And you find that one side or the other has a higher rate of failure of all their components because of the oscillation that occurs as a direct result.
Allen Hall: Create a tank circuit. Yeah. But those, again this is, as we were talking about earlier the number of electrical engineers on staff at some of these operators is like a 1%, maybe?
2 percent of the staff? 2 percent if you’re lucky. Which there are electrical machines. That’s what they do. We need to have, we need to be a little bit I don’t want to say smarter about it, but we have tools. And this is where Empath come in and where you come in and MotorDoc comes in, you have the tools.
They’re here.
Howard Penrose: And what’s really funny about it is it’s mechanical types like vibration analysts and mechanical engineers that understand the signature they’re looking at. But they hear electrical signature analysis and all of a sudden everybody’s afraid. Or they go, oh no, that’s an electrical issue, that’s for the electricians.
No, actually, the technology was originally developed to look for bearing and gear issues in motor operated valves in the nuclear power industry. It was never meant to look at rotors. It was never meant to look at all this other stuff. It was just incidental that it did it. And, um, it’s, what’s, it’s, what’s fascinating about, the technology and its application.
Allen Hall: It’s wonderful. It’s wonderful. And for those who haven’t seen the system, how do they get onto your website? How do they find you?
Howard Penrose: They can, they can go straight. The easiest way to go is motordoc. com motordoc.com and then they can go to EmpathCMS which i have some videos of wind turbine stuff or MotorDoc ai where i have a little you know podcast of maybe 50 people if i’m lucky where i talk about a lot of this and show how it works and so on so i’m trying to get the information out i published a book on it Practical Electrical and Current Signature Analysis of Electric Machinery and Systems, which includes a chapter on wind turbines.
Allen Hall: I really appreciate you being on this podcast. I like talking to electrical people that are knowledgeable and have had experience in industry for a long time because you’re such a huge resource to everybody and we need to be using you more than we probably are. But, and it’s good to get the word out, right?
Because there’s some parts of the world and some parts of America that may not have heard of you. So let’s get the word out. Hey, go check out Motordoc and get ahold of Howard because he’s a resource. Howard, thank you so much for being on the podcast.
Howard Penrose: Absolutely. Thank you.
- SEO Powered Content & PR Distribution. Get Amplified Today.
- PlatoData.Network Vertical Generative Ai. Empower Yourself. Access Here.
- PlatoAiStream. Web3 Intelligence. Knowledge Amplified. Access Here.
- PlatoESG. Carbon, CleanTech, Energy, Environment, Solar, Waste Management. Access Here.
- PlatoHealth. Biotech and Clinical Trials Intelligence. Access Here.
- Source: https://weatherguardwind.com/empathcms-fast-fault-detection-wind-turbines/